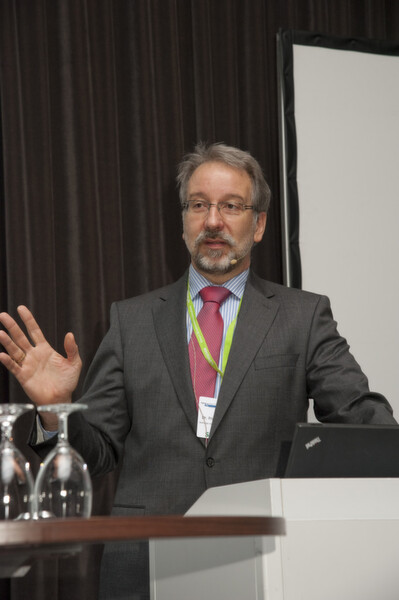
Dr Friedrich Haefele, Vice President Fill & Finish Biopharma at Boehringer Ingelheim
Dr Friedrich Haefele, Vice President Fill & Finish Biopharma at Boehringer Ingelheim talked in his keynote speech at the Pharma Congress 2016 about the revision of Annex 1 of the EU GMP Guide. Read here what the pharmaceutical industry expects form the new Annex 1.
http://www.gmp-compliance.org/enews_05326_EU-GMP-Annex-1-Revision-2016—what-does-the-pharmaceutical-industry-expect_15160,15266,15265,15432,Z-PEM_n.html
Europe’s biggest Pharma Congress of its kind took place in Düsseldorf on 12 and 13 April. With more than 1000 participants, 90 exhibitors and 10 GMP conferences this Congress 2016 has been the biggest since the first one 18 years ago. 50 lectures, almost exclusively case studies from pharmacuetical companies such as Pfizer, Novartis, Boehringer Ingelheim and many more were discussed. Special attention was paid to the keynotes at the beginning of each congress day.
Dr Friedrich Haefele, Vice President Fill & Finish Biopharma at Boehringer Ingelheim talked in his keynote speech about the revision of Annex 1 of the EU Guidelines to Good Manufacturing Practice. The first version dates already back to the year 1972. Dr Haefele stated that there had already been five revisions since this time but no fundamental review. This means the time has come to revise this fundamental document on the regulation of sterile manufacture in Europe.
Dr Haefele demonstrated the need for action on one hand by a comparison with the FDA Aseptic Guide and on the other hand by means of his own commenting. Friedrich Haefele said that priority should be given to harmonisation. He basically believes that Annex 1 should remain reserved for sterile parenteral products and that other sterile products or active pharmaceutical ingredients should be regulated in other documents or in specific annexes. He also wants a separation between aseptically manufactured and terminally sterilised products in the new Annex 1.
He considers DIN ISO 14644-1 to be a central document that is used for the classification of clean rooms in the European Guideline but also in the US Guide. Dr Haefele is not bothered by the fact that the limit for 5 µm particles has been deleted from the grade ISO 5 (ISO 4.8). According to him it should also be deleted from the European requirements. Deviations in the case of 0.5 and 5 µm particles occur essentially in parallel so that it should be possible to renounce to the limit for 5 µm particles.
Dr Haefele also proposed a simplification for the microbiological environmental monitoring. Settle plates as well as microbial air sampling are required in Europe at the moment. According to Dr Haefele only the microbial air sampling should be compulsory whereas the use of settle plates should be optional or additional. The use of average values in the microbiological monitoring in the clean room should be dismissed. With the use of isolators with validated decontamination cycles the microbiological monitoring could be reduced to the essential pursuant to ICH Q9 Quality Risk Management.
In contrast to the FDA Aseptic Guide the European Annex 1 contains requirements concerning the crimping process as well as a differentiation between aseptic and clean processes. For the latter Dr Haefele wants a clear definition of “Grade A Air Supply” that should be used for protection during the process according to Annex 1. Dr Haefele stated that the industry has its opinion concerning this but that it should also be recorded in the relevant official document. By this he meant the use of air filtered according to the requirements of grade A without considering the microbiological requirements.
There are important differences between Annex 1 and the Aseptic Guide in the area of sterilisation. The US document contains no indications for a terminal product sterilisation. It is contained in the EU document. Dr Haefele proposes to limit the requirement for a sterilisation with pure steam primariliy to the terminal product sterilisation and to also allow other methods e.g. sterilisation with ethylene oxide for example for so-called ready-to-use materials.
He sees further potential for improvement concerning the topic sterile filtration. He considers that the integrity testing after sterilisation immediately before filling can be omitted since the data of the filter validation and the integrity testing after filling give adequate security. To renounce to the obligatory integrity testing after sterilisation and before use, reduces the complexity of the aseptic set-up and when constructing facilities.
A further difference concerns the quality oversight. In Europe there is no requirement that the quality assurance (physically) must take place on-site during aseptic processes. But the Aseptic Guide requires a QC oversight and here, especially the media fill is mentioned. Dr Haefele invoked a harmonisation of the requirements, in order to strengthen the European philosophy, however. Quality assurance is a system and not an organisation. Mr. Haefele proposed a further change concerning the media fill in isolators. Here, interventions are carried out from the outside when carrying gloves. This means that they are “person-neutral”. The requirement that the qualification of interventions during the media fill has to be done person-specific should therefore be omitted for media fills in isolators.
As concerns the topic disinfection Mr. Haefele would prefer the admission of hydrogen peroxide for the decontamination of surfaces in isolators and material locks as well as the dispensation with the mandatory rotation when using disinfectants.
A further topic in Annex 1 is the monitoring of the integrity of containers containing sterile medicinal products. At the moment, the Annex requires a 100% integrity testing only for containers closed by fusion (glass ampoules and BFS containers). Dr Haefele would prefer more openness up to suitable controls for all packaging systems or pharmaceutical dosage forms.
Finally, he reaffirmed the use of modern barrier techniques for the aseptic manufacture as state-of-the-art and repeated his wish for a harmonisation of the requirements for sterile and aseptically produced medicinal products. MRA, mutual recognition agreements, could reduce the number of regulatory inspections at the companies.
Currently, the publication of the draft of the new EU GMP Annex 1 is planned for autumn 2016.
Source: Pharma Kongress 2016 (companies who wish to book a booth in 2017 can register here)
/////Dr Friedrich Haefele, Vice President, Fill & Finish Biopharma, Boehringer Ingelheim, EU GMP Annex 1 Revision 2016, pharmaceutical industry,